Strong foundation enables growth, collaboration
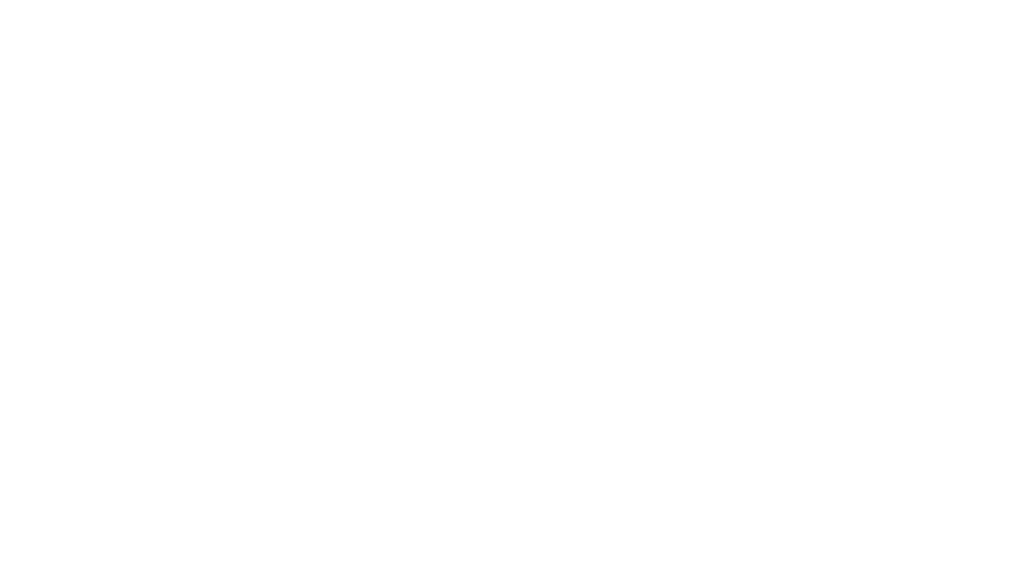
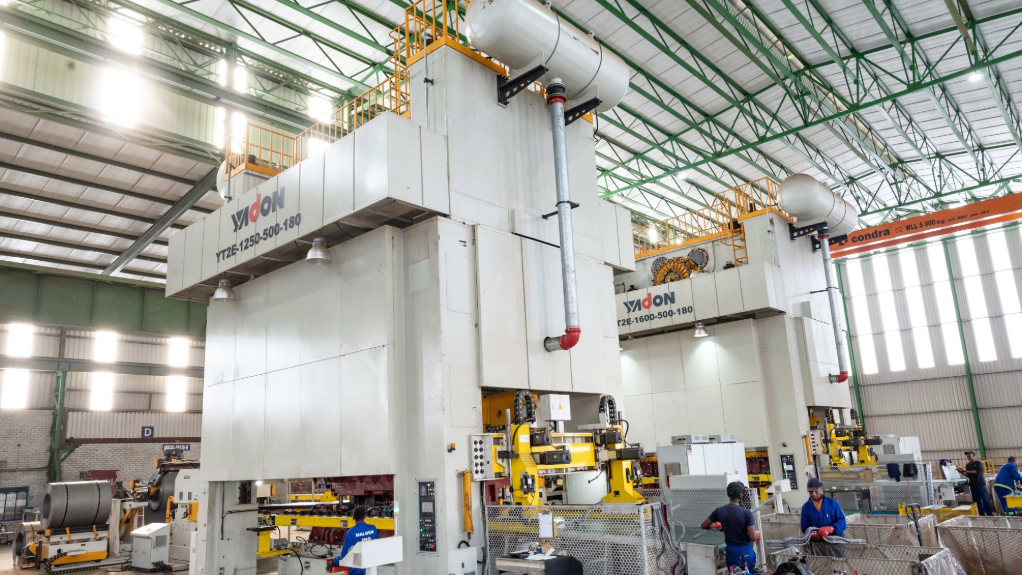
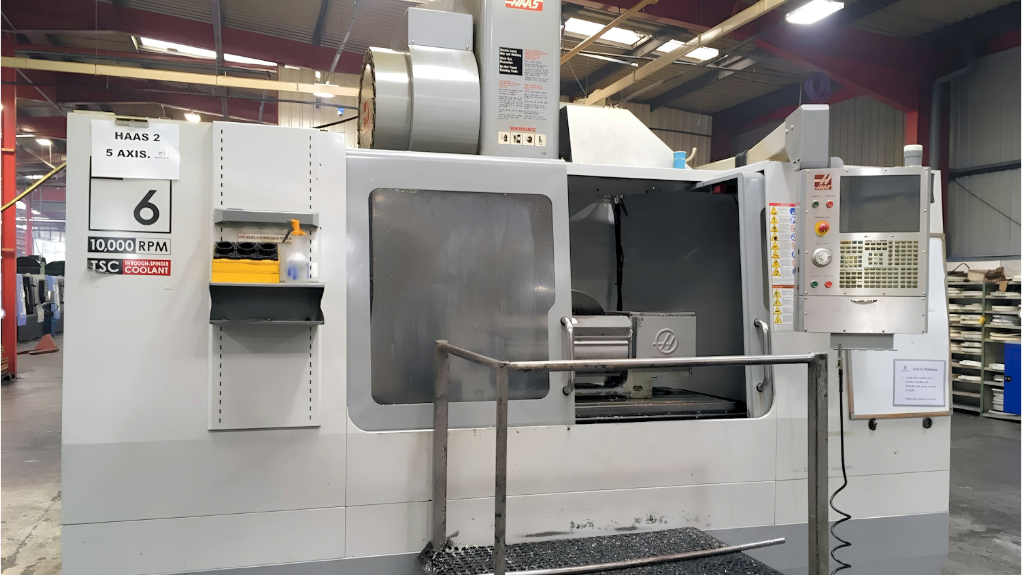
IN-HOUSE PRESS SHOP In-house computer numerical control (CNC) machining capabilities and in-house press shop with Yadon pressers accommodate all Malben Engineering’s tooling needs
MACHINING EFFICIENCY In-house machining capabilities are able to manage all large multistage tooling repairs and upgrades
Automotive components manufacturer Malben Engineering believes that a strong tool and die-making (TDM) foundation helps it collaborate with original-equipment manufacturers (OEMs) and global tool manufacturers for innovative tooling and the provision of in-house manufacturing support.
Malben Engineering technical director Marco Smargiasso says that the company’s vertical integration and investment in TDM stands as a “key differentiator” in South Africa where there is a shortage of TDM skills, and more than 80% of its manufacturing capacity is lost owing to a lack of infrastructure investment and outsourcing to international markets.
“This is according to the INTSIMBI National Tooling Initiative: a national, multi-stakeholder initiative which was established under the auspices of the Department of Trade, Industry and Competition and the Production Technologies Association of South Africa to implement a turnaround strategy for South Africa’s distressed tooling industry,” he adds.
Smargiasso attributes the local TDM deficit to a lack of economies of scale: “To have a stable TDM business, you need consistent workflow. In the automotive component sector, it tends to be a ‘feast or famine’ scenario. When an OEM launches a new vehicle, TDM is in demand, and locally there are not enough suppliers.”
He also points to there typically being a significant gap between model launches within automotive companies, with model life cycles typically ranging from seven to ten years. This is compounded by the fact that OEMs tend to carry over many parts from old to new models.
“With no new TDM demand, tool and die makers cannot survive.”
Moreover, the decline in TDM is not unique to South Africa, with Smargiasso noting that South Africa is home to seven major OEMs that make about 600 000 vehicles a year, while China’s 16 OEMs produce over 30-million vehicles a year.
“With the largest automotive industry in the world, China has out-competed TDM sectors globally and OEMs now outsource most tooling for new models to China.”
A Strong Foundation
Malben started out as a tool and die maker in 1974, and then transitioned successfully into mass automotive component production. However, unlike many current competitors, the company still retains and continues to invest in TDM as an in-house support service.
Malben’s significant step-change – expanding its manufacturing capability in 2021 and 2022 – followed the launch of new vehicle models by its largest OEM client, which required more than 200 new tools. Malben produced 40 of those tools, significantly more than its local competitors.
The company has also created a tooling facility to maintain and make replacement components for the tools used in production.
“We would not be able to run our manufacturing operation without the support of our tool room. We have invested in software and technology that keeps us relevant and competitive,” advises plant manager Jithin Kottikkal.
“Our tool room handles repairs and improvements. We have found slight discrepancies between computer-aided draughting models received from China, and the tool itself. So, we take the original and reverse engineer it, making any adjustments based on that,” he explains.
Tooling Up for the Future
Smargiasso emphasises the value of Malben’s historical experience in TDM, noting that the company uses its expertise to analyse tool designs presented by Chinese manufacturers, ensuring that designs deliver correct product quality and run capacity.
“We determine 80% of [the] project cost within the first 20% of the actual life cycle. By getting the quality and the tooling design correct up front, the home-line trials, customer sign-off and approval process goes smoothly. More importantly, it means that for the rest of the project life – normally ten years – we do not have a tool that becomes an albatross around our neck,” he says.
Malben commercial director Marius Schafer concurs, noting that the company continues to invest in intellectual property (IP) needed to manufacture “high-quality” parts – despite not being able to manufacture large tools.
“As a Tier 1 supplier, Malben’s value-add and differentiator for our customers includes meticulously reviewing the tooling for functionality, robustness, durability and in terms of process layout,” says Schafer.
This is achieved through process modelling and stamping simulations. These services were complicated by the Covid-19 pandemic, as Malben needed to liaise with a tool shop in China thousands of kilometres away, remotely.
To remain up to date, Malben is also investing in equipment, for example, planning for the installation of a new 2 500-t press.
“Because of our tooling expertise and upgraded technologies, our internal investment in people and skills, IP and in leveraging different linkages and partnerships, we can quickly pivot as required, adopting and incorporating any new technologies on the market,” Smargiasso concludes.
Comments
Press Office
Announcements
What's On
Subscribe to improve your user experience...
Option 1 (equivalent of R125 a month):
Receive a weekly copy of Creamer Media's Engineering News & Mining Weekly magazine
(print copy for those in South Africa and e-magazine for those outside of South Africa)
Receive daily email newsletters
Access to full search results
Access archive of magazine back copies
Access to Projects in Progress
Access to ONE Research Report of your choice in PDF format
Option 2 (equivalent of R375 a month):
All benefits from Option 1
PLUS
Access to Creamer Media's Research Channel Africa for ALL Research Reports, in PDF format, on various industrial and mining sectors
including Electricity; Water; Energy Transition; Hydrogen; Roads, Rail and Ports; Coal; Gold; Platinum; Battery Metals; etc.
Already a subscriber?
Forgotten your password?
Receive weekly copy of Creamer Media's Engineering News & Mining Weekly magazine (print copy for those in South Africa and e-magazine for those outside of South Africa)
➕
Recieve daily email newsletters
➕
Access to full search results
➕
Access archive of magazine back copies
➕
Access to Projects in Progress
➕
Access to ONE Research Report of your choice in PDF format
RESEARCH CHANNEL AFRICA
R4500 (equivalent of R375 a month)
SUBSCRIBEAll benefits from Option 1
➕
Access to Creamer Media's Research Channel Africa for ALL Research Reports on various industrial and mining sectors, in PDF format, including on:
Electricity
➕
Water
➕
Energy Transition
➕
Hydrogen
➕
Roads, Rail and Ports
➕
Coal
➕
Gold
➕
Platinum
➕
Battery Metals
➕
etc.
Receive all benefits from Option 1 or Option 2 delivered to numerous people at your company
➕
Multiple User names and Passwords for simultaneous log-ins
➕
Intranet integration access to all in your organisation